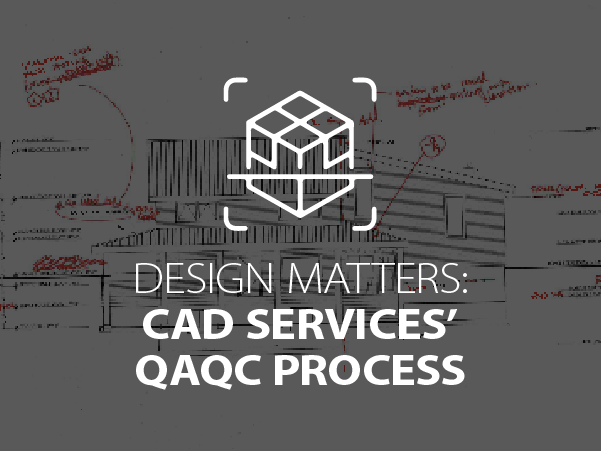
Design Matters: CAD Services’ QAQC Process
Design Matters: CAD QA/QC Review Process
Every aspect of construction begins with the design—that’s what makes accurate and detailed drawings and plans so important. Surveyors, contractors, city reviewers, and owners rely on the information they find in our drawings.
To ensure it was producing the highest quality plans and drawings for its clients, the FOCUS CAD Services Department was tasked with developing a consistent way of checking and reviewing plans so that all department team members followed predetermined standards. The standards evolved into a checklist that is printed out and used as a guide for CAD Services team members to use when they examine or inspect plans.
Redlines and Peer Review
Each drafter performs a personal review of their work and applies redlines prior to sending the plan to a team member. The next member performs a peer review of the plans, further marking the printed set with redlines and items for consideration. When needed, an in-person conversation accompanies the redlines to ensure the drafter fully understands the redlines and their intent. This conversation helps to reduce the likelihood of missed or misunderstood redlines appearing on future iterations.
Consistency Across All Plans
Because it’s so vital to improving our design drawings, FOCUS integrates QAQC into every project. “Certainly, a smaller plan may take a shorter time to review, but the items we look for are consistent across all plans,” explains Christian Broberg, CAD Services junior project manager. “We want to make sure the plans that are released from our office are clean and uniform.”
Efficiency During Review
Our engineers and CAD team know design innovations can’t reach their full potential if plans aren’t quickly approved by municipalities. Recently, a design from our office met some difficulty passing the city’s review. Though it was designed to residential code, there were changes that were required by the specific city. Our client returned to us with the feedback and sought a quick turnaround. “The needed fixes were made, and we promptly returned the plans to the client,” recounts Christian. This level of service not only improves the client experience and minimizes back-end corrections to plans, but also helps contractors easily read and understand what they should be building.
Sharpening Our Skills
The benefits of a robust QAQC program reach far beyond making every project a success. It also creates opportunities for employee training, ensuring we’re sharpening our skills as drafters and creating greater accuracy. “Each CAD team member continues to grow in knowledge and experience as they review plans and are given feedback,” Christian shares. “This serves to strengthen our capacity for accurate design.” It also increases the trust and camaraderie amongst our team. The closer we work together, the more we trust and understand that reviews are meant to make everyone’s work better and not as a hit to someone’s ego.
We focus on the quality of our plans every day and want our clients to feel the assurance that their work is being given every consideration, down to the smallest detail. By following this robust review program, our clients can experience a stress-free plan approval and build.