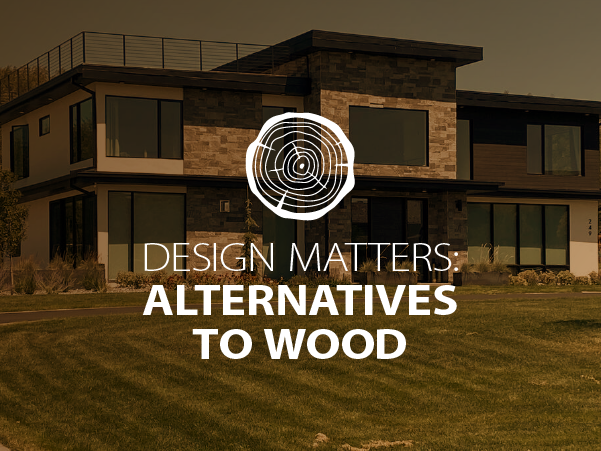
Building Without Wood: Alternatives to Lumber
Providing Utah’s Developers and Contractors Budget-Friendly Options in a Time of Shortage
In the continuing lumber shortage, many designs are turning toward wood alternatives. FOCUS Structural Engineers have found several options, from structural insulated panels and insulated concrete forms (ICF) to structural concrete insulated panels (SCIP) and light gauge metal studs. While the current cost of lumber has reprioritized these methods and resources, there are additional benefits.
According to John Charchenko, Structural Project Manager, before the shortage wood alternatives were primarily used due to their energy efficiency. “Wood studs with insulation in between are not thermally efficient, and they don’t dampen sound much,” he explained. In comparison, the insulation in most primary wood alternatives is much tighter with fewer thermal breaks. “They heat and cool more uniformly and cost less to heat and cool,” he concluded.
Steve Ostler, Structural Project Manager, agreed, and they both emphasized increased durability and strength. However, results vary depending on the alternative. Steve prefers ICF systems. “They are cost-effective, durable, and have great capacity. They also have International Code Council (ICC) testing values and are approved by the American Concrete Institute (ACI),” he said. Still, he pointed out that wood alternatives are best used where there are “tall walls and long spans on floors and roofs.”
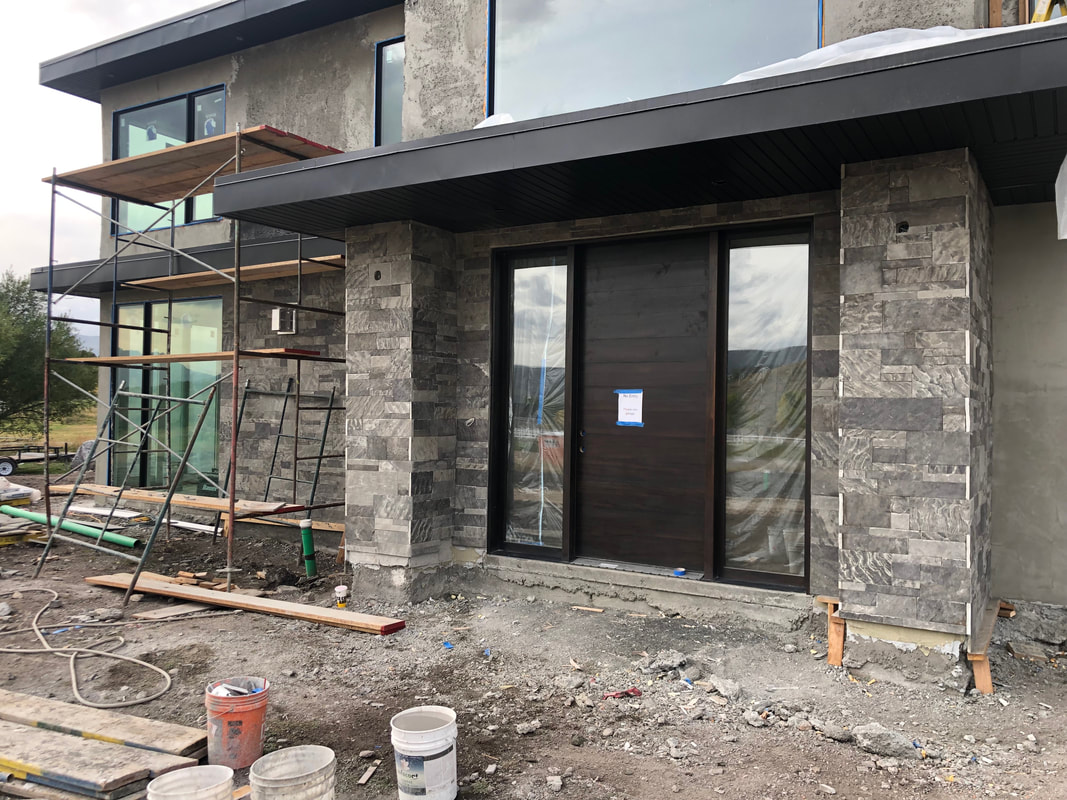
In-progress modern home in Heber with stone cladding at lower level and unfinished panel at upper level.
John prefers SCIP systems. “They can be finished in a wide variety of interior and exterior finishes and looks. Any finish that could be applied to a wood-stud home can be used on a concrete home; however, it is much more durable. It is literally bullet-proof.” Concrete alternatives, he pointed out, have a much longer life span. “They may also perform much better in a wind or seismic event.”
Because wood is organic, it will deteriorate more quickly than concrete. A building with a longer life span is more valuable, which makes a concrete building ideal for both safety and value factors.
So what’s stopping everyone from switching over? What are the challenges?
The learning curve of the new materials is most significant. “There are different tools required for each construction method,” observes Steve. Luckily, “the concepts are all standard throughout.” Still, the FOCUS team had to do a significant amount of research to build with wood alternatives properly and safely.
With this learning comes mentorship. “We’ve streamlined our design process and standardized our calculation protocols,” Steve asserts. These conventions mean the processes are easy to teach others, allowing our team to design efficiently and accurately.
“It requires a different type of construction that many contractors are not familiar with,” John continued, which is why it’s so important to have experts in the industry. “We have not shied away from learning a new system.”
Though it requires time, effort, and a strong desire to stay abreast of the innovation curve, “the advantages outweigh the disadvantages,” said John. Steve narrowed in: “As these replacements are proven to contractors, they are a way to give options to their clients that are not possible with wood.” It turns out that in a time of frequent supply chain disruptions and daunting expenses, options are worth their weight in concrete.